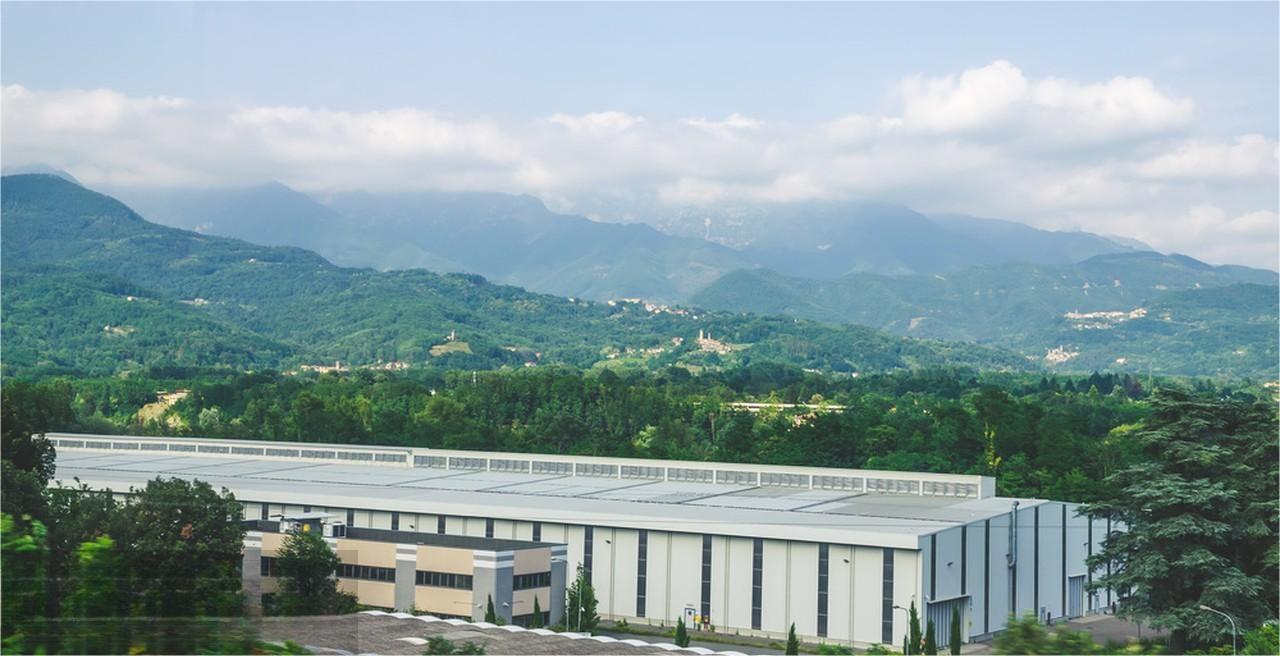
News
Corrosion resistance: The CrO coating provides an additional corrosion-resistant layer, which helps protect stainless steel materials from chemical corrosion, especially when used in harsh chemical environments. Wear resistance: The coating may enhance the wear resistance of the sealing ring, which helps to extend the service life of the mechanical seal and reduce the frequency of maintenance and replacement. Reduce friction coefficient: Coatings may help reduce friction between the sealing ring and the corresponding sealing surface, which can reduce energy loss and improve mechanical efficiency. Good sealing performance: The CrO coated sealing ring is designed to achieve a good sealing effect, preventing the leakage of liquids or gases, which is crucial in pumps, valves, and other rotating equipment. High temperature endurance: The coating may enhance the performance of the sealing ring under high-temperature working conditions, which is particularly important for mechanical seals used in high-temperature environments. Material compatibility: CrO coating may improve compatibility with different process fluids, enabling it to resist corrosion from various chemicals, including acids, bases, and solvents. Reduce maintenance: Coatings may reduce the maintenance requirements for sealing rings, as coatings can reduce wear and corrosion, thereby reducing the need for regular inspections and maintenance. Improving system reliability: By reducing leakage and enhancing sealing performance, CrO coated sealing rings help improve the reliability and safety of the entire system. Environmentally friendly: The use of CrO coating may reduce environmental risks caused by seal failure, as it reduces the leakage of chemicals into the environment.
Cyclone dust separator HWCS 2 "is a device used for cleaning aqueous liquids containing dirt and solid particles, and can transport the cleaned liquid to sealed areas or other required areas. The design features of this device include standardized design, optional housing materials, and threaded connections that meet most commonly used connection requirements
The heat exchanger of mechanical seals is an important component used to cool the mechanical seal barrier/buffer/flushing fluid, which helps to reduce the temperature of the sealing surface, thereby optimizing sealing performance and lifespan.
Low temperature bellows sealing is a sealing technology used in extreme low temperature environments, which ensures the safety of pumped fluids while providing long-term reliability. When designing pumps for transporting low-temperature fluids, special designs are often used, such as vertical multi-stage double shell pumps according to the American Petroleum Institute (API) 610 standard. These pumps have a heating chamber called a cofferdam that can thermally isolate the shaft seal from the cold pumped fluid, allowing for the use of traditional sealing techniques
The HW800 dry running bellows cartridge seal is suitable for the most common standards and extended sealing chambers of ANSI, DIN, and metric pumps. Its bellows inner diameter is designed with a 45 degree chamfer to ensure stress dissipation in each bellows plate and maximize its service life. It is suitable for pipeline sealing applications in fields such as petroleum, chemical, power, pharmaceuticals.
Famious Hanway industries' type HW606 is a high-temperature and corrosion-resistant rotating corrugated pipe component that uses different materials Including heat treated AM350 or Alloy 718 bellows, low expansion alloy sealing surface retainer, and 316 stainless steel wheel hub and housing and Inconel material. They can reliably seal fluids in harsh high-temperature corrosive environments and provide excellent sealing surface stability at high temperatures.
A fluid reservoir for a pump mechanical seal is an essential component of the sealing system, particularly for double seal arrangements. It serves several important functions: Buffering: It provides a buffer for the process fluid, preventing it from coming into direct contact with the atmosphere, which can be critical in applications where the process fluid is hazardous or toxic. Pressure Control: The reservoir can help in maintaining a stable pressure within the seal chamber, which is crucial for the proper functioning of the mechanical seal. Lubrication: It can act as a source of lubrication for the seal faces, reducing friction and wear. Cooling: In some cases, the fluid reservoir can also serve to cool down the process fluid, preventing overheating of the seal faces. Flushing: It can provide a means for flushing the seal chamber with clean fluid, which is especially important in applications where the process fluid is abrasive or corrosive. Compensation for Thermal Expansion: The reservoir can compensate for any thermal expansion or contraction of the process fluid, maintaining the correct volume and pressure within the seal chamber.
HWGS gas seals typically consist of a stationary seal ring and a rotating seal ring. The seal faces of these rings are usually made of a hard material like silicon carbide or carbon graphite, which provides a smooth, wear-resistant surface. The seal faces are kept apart by a thin film of gas, which is supplied under pressure to the seal chamber. This gas film prevents direct contact between the seal faces, reducing friction and wear, and thereby extending the life of the seal.
selecting a hand refill pump for mechanical seals, it is important to consider the specific application requirements, including the type of fluid being handled, the operating conditions, and the necessary safety and reliability features to ensure the pump meets the needs of the system it will be used in.
The HWCS1 cyclone separator operates on the principle of centrifugal separation, separating solid particles from the pump discharge pipeline and transporting them to the mechanical seal chamber through the overflow outlet point of the cyclone. This type of equipment is crucial for preventing the leakage of hazardous liquids such as crude oil and sulfuric acid, while allowing the pump shaft to rotate relative to the static pump body. The design and understanding of the geometric parameters of a cyclone separator are crucial for ensuring the cooling flow rate and pressure drop of mechanical seals, in order to ensure effective cooling and operational integrity of the sealing surface